Application 6. Turboblower
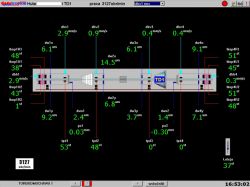
In this application, the system operates on a very special machine which is a turboblower supplying air to the iron blast furnace. As the demand for air changes frequently within wide range, the blower operation conditions vary constantly. The turbo blower output is changed by adjusting its speed within 2600 – 3350 rpm, accordingly. The changes of speed result mainly in fluctuations of bearing temperature and axial movements and, to a lesser extent, in vibration levels. Before installation of the system, the temperature and axial movement data, essential for the machine operator, was derived from analogue indicators located at a considerable distance from the operator panel and registered using conventional paper recorders. In this case, the investor decided to upgrade the existing system at a least cost, by adding signal visualisation for the operator and data archiving options with possibility of machine behaviour diagnostics. Digital recorders were considered, however, the idea was dropped due to envisaged problems with the sequential reading of data and no possibility for diagnostics. The concept of visualisation and archiving using controller based system was also rejected due to high costs and no possibility of making diagnostics since such system registers scalar (pointwise) values similar to paper or digital recorder. Eventually, optimal solution was found by using the JAD16/16 data acquisition unit with the SMMoperator software application. To keep the investment costs down, it was decided to dispense with the operator terminal while the SMMoperator application was installed directly on the data acquisition unit. Such a solution is maybe not the best one but it has been functioning since then without objections.
The following set of measurements is performed:
- 4 channels for absolute vibrations
- 2 channels for absolute axial vibrations
- 8 channels for relative vibrations, four bearings in two axes
- 14 bearing temperature measurements
- oil temperature
- rotating speed measurement
- phase marker
In spite of high frequency of records due to frequent changes in the rotation speed, by appropriate setting-up of the system it has been made possible in this particular case to survey and analyse 18-month history of machine operation; after that time the data base is archived and the oldest data is replaced with the current one.
In 2001 and 2004, two steam turbines and diagnostic testing terminal with the SMMturbo application software were incorporated into the system. Differently to the turboblower, a stand-alone operator terminals with SMMoperator is provided for each turbine. At present, four users use the system.